Australia’s national science agency, CSIRO, has opened a $6.8 million facility in Clayton, Victoria, dedicated to taking its printed flexible solar technology out of the lab and into the real world.
Unlike traditional silicon solar panels, CSIRO’s flexible solar cells are printed on thin plastic films.
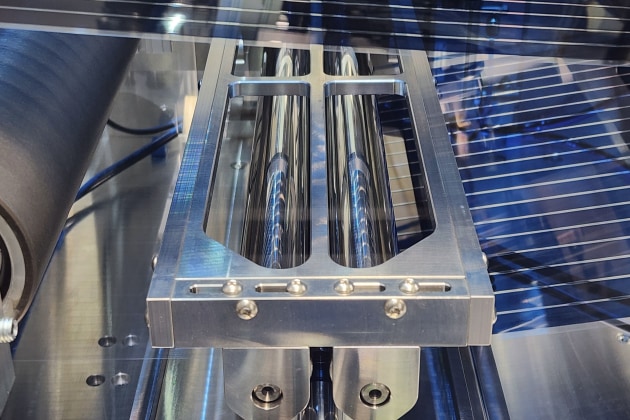
This makes them lightweight, portable, and suitable for various applications across urban construction, space, defence, mining, emergency management, disaster relief, and wearables.
CSIRO executive director, Digital, National Facilities and Collections, Professor Elanor Huntington, said the cutting-edge CSIRO Printed Photovoltaic (PV) Facility is the newest addition to CSIRO’s suite of critical infrastructure that enable the industries of tomorrow – in this case, a thriving Australian flexible solar manufacturing industry.
“Through CSIRO’s new Printed PV Facility, industry partners can access both researcher expertise and specialised equipment to improve and apply flexible solar technology in novel ways, anywhere there is sunlight,” Huntington said.
“This not only offers incredible opportunities for Australian manufacturers but also contributes to addressing global energy challenges and advancing the transition to net zero.”
Leader of CSIRO’s Renewable Energy Systems Group, Dr Anthony Chesman, said printed flexible solar is not intended to replace silicon rooftop panels, but rather to complement them.
"This printed solar technology unlocks entirely new applications for affordable, versatile and sustainable energy generation," Dr Chesman said.
CSIRO’s innovative solar cells are made using an advanced material called perovskite, which is printed on long continuous rolls of flexible film.
"Our new system is highly automated. The multiple printing and laminating steps are performed in a single continuous operation, which significantly cuts down on production costs and the upfront investment needed to get started,” Chesman said.
“Our team has also developed an automated system that can produce as many as 14,000 test solar cells a day to fine-tune their design and performance.
“We’re looking for partners who want to join us on the R&D journey and ultimately take this technology to market.”
In addition to printed flexible solar, the lab is equipped to explore other fields that use printable materials for battery and hydrogen technologies, opening doors to a wider range of innovative applications.