The world’s first carbon neutrally produced whiskeys are being distilled using Oilon heat pumps.
The unique zero-emission distillation process of the Irish distillery has been implemented with a comprehensive system design applied from the process industry.
At the core of the design are Oilon's high temperature heat pumps, which utilise all waste heat.
Ahascragh is a two-hour drive from Dublin, and the distillery is based in a former brick mill, a building that is more than 200 years old.
The historic building re-opened as a whiskey distillery in the summer of 2023, according to the owner of Abascragh Distillery, Gareth McAllister.
‘Distilling whiskey is very energy intensive: Each bottle of traditionally distilled whiskey produces 3-4 kilograms of carbon dioxide emissions. Now, we are proud to be able to offer consumers a whiskey alternative whose production has not harmed the environment,” he said.
“Unlike other distilleries in Ireland, heat is provided to the distillery through heat pumps which means that there will be no flue related emissions or impacts on the local environment.”
Ireland produces plenty of green electricity: In 2022, 34 per cent of the country's electricity production (about 13.2 TWh) was wind power.
Instead, thermal energy in the island state is still largely produced with fossil fuels. Even thermal energy used in whiskey distillation has traditionally been produced with natural gas.
‘In Ahascragh, the heat needed for the process is produced by high temperature heat pumps instead of natural gas. The pumps are powered by wind-generated electricity,” McAllister said.
“In this way, we have been able to get rid of fossil fuels and the process has become zero-emission.”
Finnish technology company Oilon has delivered two P450 series heat pumps and one smaller P150 heat pump to the distillery.
P450 series pumps are capable of producing temperatures of up to 120 degrees. At Ahascragh the design temperature is 115 degrees.
Irish company Astatine which specializes in carbon-neutral turnkey solutions was responsible for the overall design of the system.
Two parallel processes work in the distillery: the actual distillation process where alcohol is alternately steamed and condensed in a closed circuit, and the automatic cleaning process of the equipment, which requires a significant amount of warm water.
Astatine manager, Tom Marren, said the total COP has been raised to an exceptionally high level by applying the operating methods of the process industry.
“Heat pump technology is combined with process know-how, i.e., all generated waste heat is recovered with the pumps and utilized at another point in the process,” Marren said.
“The heat pump design, heat recovery and thermal storage means that the energy inputs to the distillery are a third of what is required with traditional technology.”
At the high temperatures of the P450 pumps, the distillation process itself is running. In this process the alcohol alternately vaporizes and condenses in a closed circuit.
The pumps are equipped with separate heat exchangers which also produce lower temperature water for the washing process. The smaller P150 pump produces domestic hot water which can be used for additional cooling of the distillation process if necessary.
Oilon sales & marketing manager, Sami Pekkola, said comprehensive system planning and the combination of processes was crucial in terms of COP and reducing emissions.
The total COP for the process is an astounding 6.5.
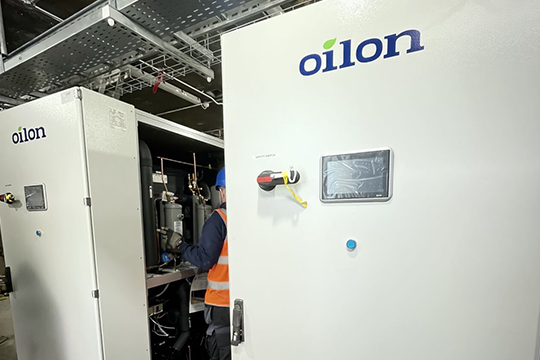
In other words, for every kWh of electricity used by the heat pump, it generates 6.5 kWh of energy for use in the process,” Pekkola said.
“This level of energy efficiency is exceptional and it can only be reached by utilising the energy flows in the process optimally.”
Oilon is a 60-year old family business which manufactures heat pumps and specialises in low emission combustion technology.