Baltimore Aircoil Company business manager, Neal Walsh and global sales development manager, Robert Downey, provide tips on how to design and operate water cooled equipment.
Evaporative cooling towers play an important role in green buildings by significantly reducing energy consumption when they supplement or replace traditional air conditioning systems, thereby reducing carbon footprint and operating costs. Although evaporative cooling is great at saving energy, it does consume some water but the benefits on energy savings outweigh the water usage, which in some places is a scarce resource.
Water conservation is therefore a high priority in designing and operating water-cooled equipment and plays an important role in Green Building Council’s Leadership in Energy and Environmental Design (LEED) certification and other sustainability programs. LEED assigns credit points to reduce water usage.
Two Design Paths
The LEED options for reducing potable water consumption in cooling towers can be separated into two strategies.
Get more use from the potable water. The first strategy is directed at maximising the use and value of each gallon of potable water used in evaporative cooling by optimising the cooling tower’s cycles of concentration (COC). The success of this strategy and the ease or difficulty of implementing it is highly dependent on the quality of the available potable water.
Substitution of non-potable water. The second LEED recommended strategy — which can be combined with the first — is to substitute non-potable water, such as HVAC condensate or rainwater, for some portion of the total water consumed. Analogous to the use of solar and wind as “alternative energy” sources to replace or supplement fossil fuel consumption, the use of non-potable water acts as an “alternative water” source, replacing potentially scarce drinking water. Obviously, the viability of this approach depends on the types of available non-potable water sources.
For some of these design paths, achieving the desired reduction of potable water use comes with some potential side effects and new challenges that must be evaluated and addressed. For instance, increasing the COC is more difficult when the local water has high hardness. Another example is HVAC condensate and rainwater that are often great naturally-soft options for non-potable water. It should be noted that these introduce the potential problems of airborne particulates that foster biological growth and of corrosiveness to the cooling equipment.
Water Consumption in a Cooling Tower
To understand the principle of COC, we must step back and understand the causes of water loss in a cooling tower (see graphic).
Evaporation: Water vapour is a major byproduct of evaporative cooling, and the Environmental Protection Agency (EPA) estimates that about 1.8 gallons of water are evaporated for every ton-hour of cooling.
Drift, leaks and overflow: While evaporation is considered a necessary and acceptable cause of water loss, other means of water loss must be carefully controlled.
Drift is the small quantity of water in the form of mist or water droplets that is blown off the cooling tower with little or no beneficial cooling effect. Equipment manufacturers address this by including drift eliminators, which control drift loss between 0.05-0.2 % of the water flow rate through the cooling tower. For a 500 nominal tonne application with 1500 gpm flow, drift loss could be up to 3 gpm, which is typical for crossflow units and represents around 1% of the total water usage.
Leaks or overflow should not regularly occur in a properly operated and maintained cooling tower. Overflow alarms should be installed at the overflow drain, as is typically required by plumbing and building codes, to quickly correct any leak or overflow issues.
Blowdown: This leaves one remaining cause of water loss. Blowdown, also known as bleed, is the water that is bled from the system to keep the concentration of dissolved solids in the circulating cooling water within acceptable limits. As water evaporates, the water escapes but most of the other molecules are left behind. This process elevates the concentration of total dissolved solids (TDS) remaining in the system water, including calcium, magnesium, chloride, and silica. High concentrations can cause scale to form or lead to corrosion, resulting in system inefficiencies, failures and maintenance headaches. The concentration of suspended solids from airborne particulates and other sources also increases, facilitating biological fouling and risking bacterial growth.
Simply put, the concentration of TDS and suspended solids is controlled by the removal of blowdown water. To maintain the optimal volume of water in the system, the total volume of water that is lost through this blowdown and through evaporation is replaced by “make-up water” (assuming no loss from drift, leaks, and overflow).
Maximising Cycles of Concentration
A fundamental measure of cooling tower efficiency is cycles of concentration, also known as concentration ratio. Cycles of concentration (COC) is defined as the ratio of the dissolved solids (conductivity) in the tower water to the dissolved solids (conductivity) in the makeup. This is easily and commonly determined by taking the specific conductance of the cooling water and dividing it by the conductance of the makeup. The calculation can also be done using minerals that are not affected by the chemical treatment regime, such as chloride or silica.
An alternate, equally accurate method, of calculating COC is to take the make-up water volume and divide it by the bleed volume. This is easily done if the tower is equipped with water meters on the make-up and bleed lines, a practice that is highly recommended.
The better the quality of the make-up water — in other words, the lower the TDS, suspended solids, and corrosiveness — the higher the COC that can be achieved and less blowdown is required to maintain the desired COC to keep the system water quality within acceptable limits. Below, we look at various methods for improving the quality of the make-up water.
TDS, and specifically water hardness, is by far the most significant factor affecting strategies to conserve water by increasing the COC. Increasing COC is much easier to implement in locations where water is naturally soft.
In LEED version 4.0, achieving at least 10 COC earns 2-4 credits, depending on whether the system is for new construction, an existing building, or a data centre. Water reduction programs achieving less than 10 COC will earn only 1-2 credits (unless at least 20% of the make-up water is recycled non-potable water, in which case 2-4 credits can be earned). (See graphs)
LEED version 4.1 is somewhat different. It removes the 10 COC threshold and instead awards credits based upon exceeding COC by a percentage. The percentage compares the COC before and after measures are taken to improve the quality of the make-up water. For BD+C and core and shell projects, exceeding the baseline COC by 25% earns 2 credits, and for core and shell an additional point can be gained if the baseline COC is exceeded by 30%.(See graphs).
Non-Potable Water as an Alternative Source
Where available, non-potable water sources can be a great way to conserve potable water, and a path to earning 2 LEED credits. Let’s look at four common categories of non-potable water: HVAC condensate, rainwater and stormwater, recycled municipal water, and grey water.
HVAC Condensate: High humidity and high cooling loads during most of the year affords a high potential for condensate capture.
HVAC condensate is an ideal source of make-up water for cooling towers for two reasons. First, the timing of the generation of condensate from air conditioning systems aligns well with the timing of need for make-up water for the cooling towers. This alignment means that a storage tank may not be necessary. Second, condensate water is pure with a very low dissolved mineral content. However, a potential downside of HVAC condensate is that it sometimes contains heavy metals, such as copper or lead, which may require treatment prior to use as make-up water.
Rainwater: Rainwater and stormwater are commonly harvested from roofs and hard surfaces, such as roadbeds or parking lots. Regulations vary by state on the use of such water. A 2012 study published by the University of Tennessee concluded that a high number of COC can be achieved with rainwater because dissolved solids are significantly lower than in tap water.
However, rainwater pH frequently is around or below 6 and therefore needs to be mitigated before use in a cooling tower to minimise the risk of corrosion and contamination. Also, control of microbiological growth must be included in any water treatment plan where harvested rainwater is being used. The level of treatment required for harvested rainwater depends on the source. Two common issues are bird droppings if the rain is harvested from a roof and oil if harvested from roadbeds and parking lots.
Recycled Municipal Water: Local municipalities are increasingly developing the capability to reclaim and sell treated wastewater (at a significantly lower price than potable water) rather than discharging it into a lake or river. “Purple pipe”, along with appropriate signage, is used to distinguish such distribution systems from potable water lines.
This water is often good quality, although the concentration of minerals is usually higher than potable water. An advantage is that the increased silica, alkalinity, hardness, and phosphate content in reclaimed water are often less corrosive than tap water. When using recycled municipal water, water quality management teams need to evaluate how corrosion inhibitors from the municipal process may impact water treatment strategies for cooling tower make-up water.
Grey Water: Unfortunately, typical commercial sources of grey water – e.g. urinals and laundry – are not appropriate for use as a direct non-potable water source without significant further treatment. Soaps found in laundry can be problematic because they act as a food source for microbiological growth.
Addressing water quality challenges
Depending on the quality of the water available, and based upon testing and recommendations of water treatment professionals, the strategy for conserving water may require the implementation of one or more mitigation methods. These methods divide into two basic categories: (a) improving the water with chemical treatment and filtration, and (b) protecting the system with materials of construction that offer high protection from corrosion.
Dissolved Minerals: Water with high mineral content can be particularly challenging because high levels of calcium, magnesium, alkalinity and silica increase the risk of scale on heat transfer surfaces, which can rapidly degrade system performance. On the other hand, high levels of chlorides and sulfates increase the risk of corrosion on various metals used in cooling water systems, which could lead to increase maintenance costs and reduced asset life. Limiting dissolved solids is critical to achieving increases in the number of cycles of concentration. Three mitigation methods are commonly used:
Chemical treatment: Scale inhibitor chemicals cause a process called crystal modification to occur, which softens the hard edges of the crystalline precipitate into rounder material that stays in solution longer and is less likely to form scale. Chemical treatments also include dispersant polymers that coalesce and agglomerate these softer particles, and by hydrophilic and hydrophobic forces make these particles less likely to bond to the heat transfer surfaces. These chemical treatments work, but they have limits based on modern chemistry, and are often insufficient to address water with high mineral content.
Mechanical Pretreatment: Most facilities need to consider mechanical pretreatment, either water softener systems or partial reverse osmosis systems or a combination of the two. Water softeners use an ion exchange resin, which collects calcium and magnesium, along with a brine tank, which uses salt as a regenerant. These systems are relatively simple and have a low total cost of ownership, but they only remove calcium and magnesium and not other dissolved solids like chlorides; and they do not reduce alkalinity. Water softeners can increase cycles of concentration from approximately 2 to 4, but rarely allow for the large leaps necessary to reach 10 COC.
Partial reverse osmosis (RO) is more effective. Water is pushed through a membrane, removing 95-98% of all minerals. Normally RO is used to produce pure water, but that would be too corrosive for cooling tower applications. Therefore partial RO is used, which blends the RO water with municipal make-up water. For water with very high mineral content, the most cost-effective design is to use a water softener to remove the hardness minerals prior to the RO process.
Suspended Solids: The concentration of suspended solids from various water sources and from airborne particulates collecting on the cooling tower facilitates biological fouling and risks dangerous bacterial growth. For this application, cyclonic filtration is more effective and easier to maintain than sand filtration.
The most cost-effective solution is to design and install a side stream filtration system with basin sweeper piping. The system should be factory assembled and delivered with the new cooling tower. (Aftermarket systems require removing the fill pack which increases the risk of damage to the fill.)
Corrosion: Water conservation strategies often involve elevated corrosiveness of the system water, especially when using partial RO or high purity non-potable water such as HVAC condensate and rainwater.
Alternative Materials of Construction: Another mitigation strategy is to select a material of construction for the cooling tower that offers some protection from corrosion, such as stainless steel. For the highest level of corrosion protection, polyurethane basin coatings can be applied. The TriArmor Corrosion Protection System from Baltimore Aircoil Company offers a factory applied polyurethane coating.(See graphic).
Multiple Design Paths
Owners and operators that address scale, bacteria, and corrosion will maintain peak system efficiency and extend the life of the evaporative cooling equipment. The published tables summarise considerations to meet these objectives.
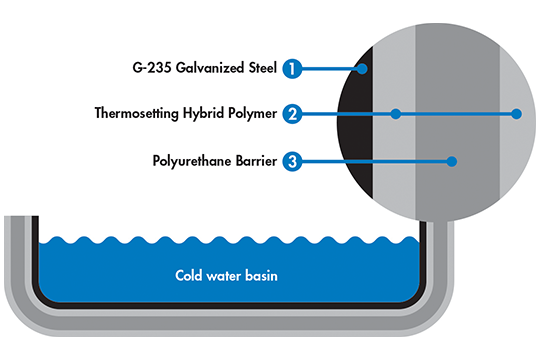
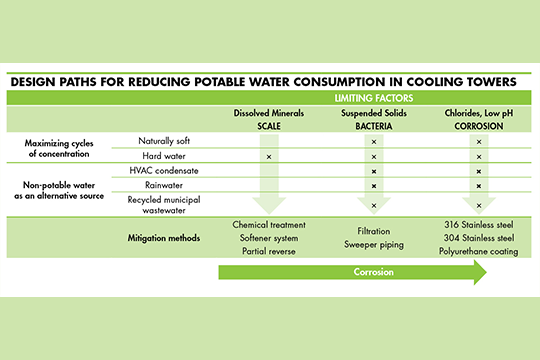
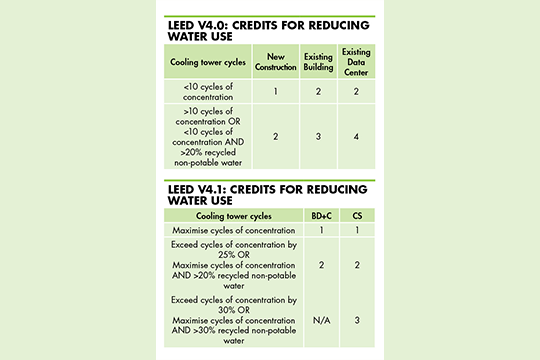